Il ruolo del monitoraggio energetico in un'azienda farmaceutica
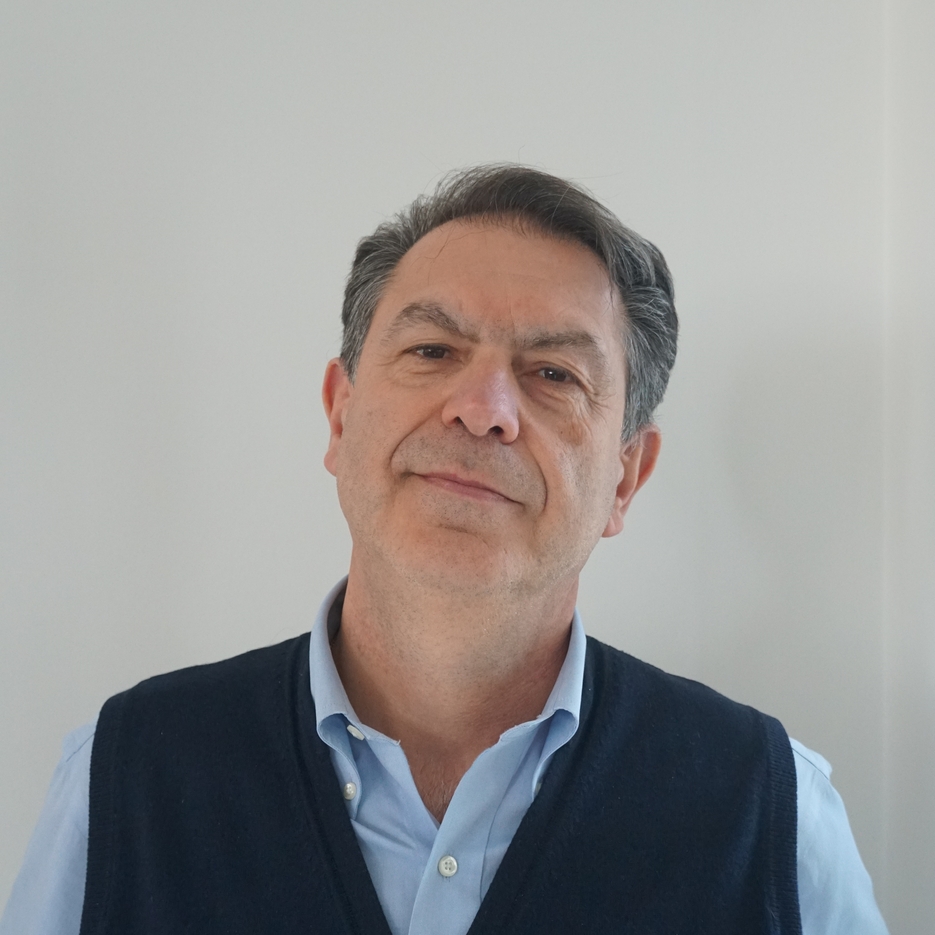
Come si può leggere nella guida operativa di Enea e Farmindustria per la redazione delle diagnosi energetiche, quello farmaceutico è un settore energivoro, dove l’incidenza dei consumi di energia sui costi produttivi è notevole e risulta ancora più rilevante in un periodo critico come questo.
La monografia, che fa parte della collana “Quaderni dell’efficienza energetica”, evidenzia come l’incidenza di consumi ausiliari tra cui, ad esempio, la climatizzazione, la produzione di freddo e i sistemi HVAC abbiano un peso predominante, fino al 70%, sui consumi dell’intero stabilimento produttivo.
A dimostrazione di questa peculiarità del settore, la quasi totalità dei possibili interventi di efficientamento energetico è ascrivibile ai servizi ausiliari: produzione del freddo e del calore di processo, produzione dell’aria
compressa, dell’acqua purificata e pompaggi.
Tali interventi, qualora realizzati, porterebbero a un risparmio energetico di oltre 11 ktep/anno che equivalgono al consumo elettrico medio annuo di circa 22 mila famiglie.
I vettori energetici nelle aziende farmaceutiche
La produzione del farmaco richiede un’atmosfera con un elevato grado di pulizia, nonché condizioni operative, in termini di temperatura e umidità relativa, particolarmente stringenti e fisse durante tutto l’anno. Questo comporta grandi spese per la climatizzazione e purificazione dell’aria, oltre che una gestione attenta delle condizioni operative.
Ad esempio, alcuni prodotti, come i farmaci iniettabili, richiedono la sterilizzazione dei macchinari e/o dei recipienti in cui avviene la miscelazione, nonché dei recipienti in cui il farmaco viene confezionato (fiale, siringhe). Inoltre, alcune fasi dei processi possono richiedere immagazzinamento a temperature molto basse, o liofilizzazione del prodotto.
Tutte queste specifiche tecniche implicano la produzione e la fornitura di:
-
calore sotto forma di vapore o acqua calda;
-
freddo sotto forma di acqua fredda o gelida;
-
aria calda secca.
Analizzando i vettori energetici acquistati dai siti produttivi farmaceutici, si nota come poco più del 60% dei vettori acquistati è relativo al gas naturale mentre solo il 35% si riferisce all’energia elettrica; la restante percentuale (3,5%) è composta da biomassa, gasolio e altri vettori energetici utilizzati in minime quantità.
La situazione cambia in modo radicale se si analizzano i vettori energetici utilizzati all’interno del sito produttivo: il vettore energetico predominante diventa l’energia elettrica, che passa dal 35% in acquisto a circa il 60% nell’utilizzo, a discapito del consumo di gas naturale che si riduce da più del 60% in acquisto a meno del 25% in utilizzo.
Le peculiarità del settore
Nell’industria farmaceutica i consumi energetici si concentrano principalmente nei servizi ausiliari. Questa peculiarità è dovuta agli elevati consumi per il trattamento dell’aria negli ambienti produttivi. Il settore farmaceutico, infatti, deve rispettare elevatissimi standard di qualità dell’aria per evitare la contaminazione dei prodotti farmaceutici.
Per quanto riguarda le attività principali (linee produttive, confezionamento, magazzini e laboratori di ricerca e sviluppo e controllo qualità), vi è un peso leggermente superiore del consumo elettrico a discapito di quello termico dovute alla presenza degli impianti produttivi, che per loro natura privilegiano il consumo elettrico. Situazione opposta analizzando i servizi ausiliari, dove rispetto al consumo totale, vi è un’incidenza maggiore del consumo termico rispetto al consumo elettrico.
I benefici dell'efficientamento energetico
L’ottimizzazione e la riqualificazione degli impianti farmaceutici attraverso l’efficientamento energetico e un asset sempre più green possono portare benefici nel medio e lungo periodo.
In particolare attraverso l’installazione di hardware e software specifici è possibile monitorare e controllare la temperatura, ottimizzare gli impianti in modo efficace ed efficiente e ottenere benefici economici.
I punti principali da tenere in considerazione sono quattro:
-
Manutenzione e controllo della temperatura, un fattore cruciale specialmente nei periodi estivi, poiché le temperature elevate e l’umidità possono compromettere la qualità dei farmaci, gravando sulla salute dei pazienti.
-
Ottimizzazione degli impianti e dell’energia consumata, riducendone l’utilizzo mantenendo comunque attiva la produzione. Con l’ottimizzazione delle tecnologie hardware e software, anche attraverso l’aiuto dell’intelligenza artificiale per l'energia, è possibile rendere gli impianti più efficienti e sfruttare le risorse in modo sostenibile.
-
Manutenzione e controllo degli impianti e prevenzioni delle anomalie: grazie all’installazione di sensori per il monitoraggio dello stabile e delle sue aree si possono controllare i consumi, individuare le aree più energivore o critiche e anche prevenire eventuali anomalie negli impianti.
-
Ottenimento delle certificazioni energetiche, ovvero di documenti che attestano la classe energetica dell’impianto e delle eventuali detrazioni fiscali e incentivi per l'efficientamento energetico.
Scopri il nostro caso studio a riguardo